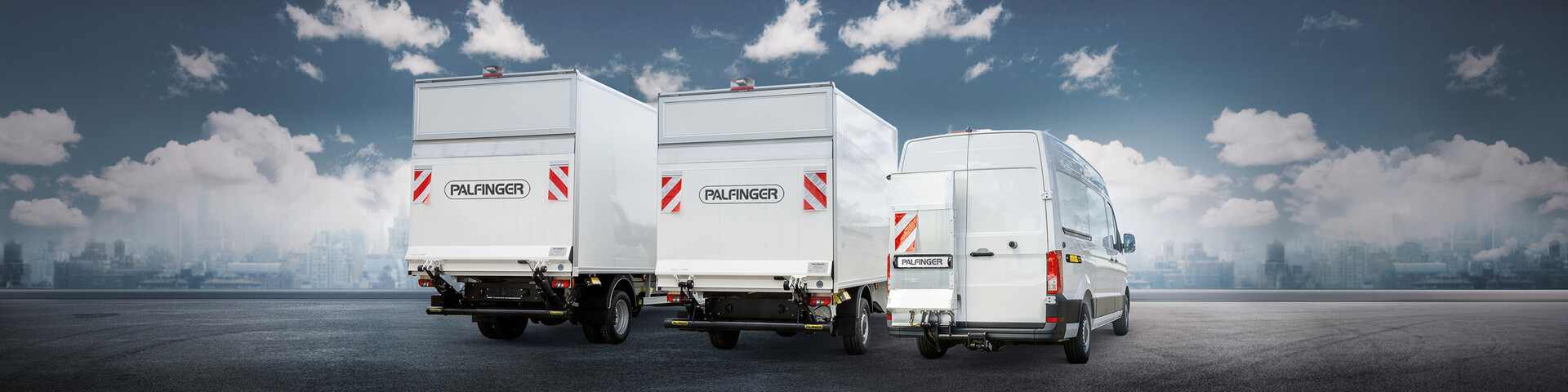
- Home
- Products
- Tail Lifts
- Service
Service
SPARE PARTS ORDER
You can easily order your spare parts in our online shop. By entering your lift serial number you will be shown exactly those spare parts that are used for your lift.* Now you can place your order whenever you want! It pays off – we grant you a 3 % discount on all online orders.
Follow here for the Onlineshop PALFINGER Tail Lifts.
Feel also free to contact our qualified staff:
Phone : +49 4221 853-355
Monday to Thursday : 7:30 am till 5.00 pm
Friday: 7:30 am till 4.00 pm
A fast and easy fax order could be done via Faxform.
* Valid for PALFINGER Tail Lifts as of serial number 8xxxxxxx.
TECHNICAL SUPPORT
Following the delivery of a tail lift, customers require comprehensive service support for many years to come. In order to meet these demands the best way and to serve as your dependable partner whenever you may need us, we have introduced an extensive online resource tool for your convenience. Our online customer service resource tool offers you comprehensive service, information and order forms.
Feel free to use the following options:
- Order spare parts online
- Get answers to frequently asked questions
- Submit warranty claims
- Select training dates
Do you prefer a personal contact? Then give our service hotline a call: +49 4221 853 355.
MOUNTING STUDIES
Before placing an order, it is important to properly assess the technical data for mounting on the vehicle. We have a team that deals exclusively with different assembly situations to decide how the tail lift has to be installed on the vehicle and which tasks have to be considered when special equipment is used.
You can get a personal mounting proposal for your project, if you fill in the document given below completely and send it back to us (Fax no. +49 4221 853-345).
TROUBLESHOOTING
Do you need technical support or documentation? Please contact us by phone (+49 4221 853 355)
Wiring diagrams are also available in our online portal.
IMPORTANT INFORMATION:
Every tail lift from PALFINGER Tail Lifts is supplied with a specific electrical and hydraulic diagram for the respective tail lift type. These documents are located directly next to the circuit board in the main tube.
You will find direct help on the following points here:
- Identification and classification of the tail lifts
- Electrical and control system
- Hydraulics
- Cylinder setup and repair
- Emergency functions
- General maintenance and service tips
IDENTIFICATION AND CLASSIFICATION OF THE TAIL LIFT TYPE
Tail lifts differ in a few, but decisive features. It is therefore important to know the exact type of your tail lift in order to, for example
- Order the right spare parts
- or to determine the correct electrical and hydraulic plan
THE MOST IMPORTANT DIFFERENTIATING FEATURES INCLUDE
- the load capacity (e.g. 1000 kg for a standard load distance)
- the tail lift model (e.g. Cantilever / Foldable / Retractable / Vertical)
- the year of manufacturing (relevant for technical developments and model adaptations).
This information can be found on the type plate of your MBB tail lift. The type plate is usually attached in two places:
- on the rear of the platform
- on the mounting tube / main beam – attached either on the top of the driver’s side or on the underrun protection
In addition, there should always be an inspection logbook in the vehicle documents. This is required for routine inspection according to the European machine norms and will be checked by a certified expert.
ELECTRIC AND CONTROL SYSTEM
The control systems of our tail lifts have been continuously developed over the last few years. The focus has been on ergonomic aspects as well as economic and technical requirements. The MBB Control system is a real benchmark in this area - it can be used in all PALFINGER Tail Lifts across all series, setting the benchmark in terms of ease of use, efficiency and reliability.
CURRENT PALFINGER TAIL LIFTS CONTROL SYSTEM TYPES
• MBB Control Eco, Plus or Premium
• Basic E
Hydraulics
The hydraulics in our tail lifts are reliable and based on a system that has been tried and tested over many years. A quick glance at the hydraulic diagram of the respective type makes it easy to understand how it works. Our standard hydraulic diagrams can be found in the operating instructions. In addition, each tail lift comes with an individual electrical and hydraulic diagram - this is located directly next to the control board in the main beam.
CYLINDER SETUP AND REPAIR
The cylinders of all our tail lifts are made by us exclusively in-house. This enables us not only to offer you all components as spare parts, but also to guarantee the proven PALFINGER quality that has been in place for decades and to continuously develop it further.
In the following section, we will show you how to replace the seal kit of the tilting cylinders. The repair can be carried out directly on the vehicle; it is not necessary to remove the entire cylinder. It takes about an hour and can be carried out by a single person: Guide to replacing a seal kit
EMERGENCY FUNCTIONS
In the event of a malfunction on the road, the top priority is to get the vehicle out of the danger zone. The controls of the tail lifts from PALFINGER Tail Lifts make it possible to deactivate unnecessary consumers in order to eliminate possible sources of interference. This enables systematic troubleshooting - the tail lift can be put into transport position and the vehicle can be transferred to a service or partner company as quickly as possible.
ACTIVATING EMERGENCY MODE
For the K, K-Plus, K-1 Plus, MBB Control and Basic E series
In the event of a defective sensor, the tail lift can be moved via emergency operation - sensors are no longer queried.
Operation via one- or two-hand control:
- Press the “Open”, ‘Lower’ and - if available - the “Additional switch” buttons simultaneously
- Hold these down for at least 10 seconds
Operation via Slimpanel:
- Press the additional button and any three function buttons simultaneously
- Press and hold for at least 10 seconds
- “E” appears in the 7-segment display - the tail lift is now in emergency mode
- Automatic processes are deactivated
IMPORTANT NOTE ON EMERGENCY OPERATION: Risk of material damage in emergency operation!
All sensors are deactivated in emergency mode. The tail lift can move beyond the set limit positions - this poses a risk of material damage!
- Observe all movements carefully
- Release the operating elements when the tail lift reaches an intended position.
CLOSING THE PLATFORM IF ALL CONTROL PANELS FAIL
If the tail lift cannot be controlled via the operating elements even in emergency mode, it is possible to close the platform manually. To do this, actuate the motor contactor and valve S5 directly on the hydraulic unit - this allows the platform to be moved in safely and the vehicle to be made ready for use again.
Access to the hydraulic unit
For tail lifts with slide-in unit
- Open the right-hand cover of the stand tube
- Loosen the fixing bolt of the hydraulic unit on the stand tube.
- Pull out the hydraulic unit until the motor contactor and valve S5 are accessible.
For tail lifts with box-type, universal or reversible unit
- Loosen and remove the unit cover.
Lifting the platform
- Bypass contacts 1 and 2 on the motor contactor until the platform has reached the loading height.
Closing the platform
- Bypass contacts 1 and 2 on the motor contactor.
- Actuate valve S5 at the same time by pressing it in, e.g. using a screwdriver.
Completion of the process
For tail lifts with slide-in unit
- Slide the hydraulic unit back into the stand tube and fix it with the fixing screw.
- Close the right cover of the stand tube.
For tail lifts with box-type, universal or reversible unit
- Put the unit cover back on and secure it.
GENERAL SERVICE ADVISOR
Regular maintenance is essential to ensure that your tail lift works reliably over the long term. It starts with simple measures such as lubricating the bearings and checking the cap bolts and extends to checking the hydraulic hoses and hydraulic oil, as well as checking the electrical components. On this page, we have compiled useful tips and recommended measures that you should observe during the daily use and maintenance of your tail lift.
SERVICE AND MAINTENANCE
In general, your tail lift should be maintained as required and regularly subjected to a professional service.
TASKS | DAILY | DDEPENDING ON USE | MONTHLY |
ANNUALY |
Checking the effectiveness and presence of the safety and warning devices |
x |
|||
Cleaning the tail lift |
|
x | ||
Checking the battery |
|
x | ||
Checking the carbon brushes on the electric monitor |
|
x | ||
Check the oil level and top up if necessary |
|
x | ||
Checking the bolts and nuts for tightness |
|
x | ||
Lubricating the low-maintenance bearings |
|
x | ||
Changing the oil |
|
x |
IMPORTANT PRACTICAL TIPS:
- Grease bearings regularly: All bearing points should be greased according to the intensity of use to avoid unnecessary wear.
- Oil change recommended annually: The hydraulic oil should be changed annually, e.g. before winter.
- Check carbon brushes: Carbon brushes are wearing parts. Depending on the frequency of use (single or multi-shift operation), an inspection is recommended 1 to 4 times a year (damage due to worn carbon brushes is not covered by the warranty)
You will find the complete maintenance and service schedule in your inspection booklet.
Lubricants and operating fluids
Hydraulic oil – Recommendations
Standard version:
Shell Tellus S2 V 15
Operating temperature: –20 °C bis 60 °C
Special configuration „cold“:
Aero Shell Fluid 41
Operating temperature: –54 °C bis 90 °C
Lubricating grease/oil – Recommendations
For bearings on the tilt and lifting cylinders
• Shell Gadus S2 (heavy-duty grease)
• Comparable grease
For movement rails on retractable tail lifts:
• Interflon Grease OG
• Comparable grease
For plastic bearings:
• Interflon LUBE EP+
• Comparable lubricating oil
WARRANTY FORM
For quick and easy preparation of our warranty claim, our e-claim service is now available at www.eetk.eu.
Simply follow the e-claim link in the menu.
If you have further questions, please do not hesitate to contact our Customer Care team.
SERVICE TRAINING
ONLINE Trainings
TRAINING other PALFINGER locations
Currently there are no trainings on other PALFINGER locations.
Please direct e-mail inquiries to seminarembb@palfinger.com
GOALS AND CONTENT OF PALFINGER TRAINING SESSIONS
In our fast-paced world of continuous change, technical equipment and facilities are changing just as quickly – and with greater frequency than was once the case. Ongoing improvements are continuously being integrated into technical systems because basic components and electronic devices are now available with higher levels of capacity. New materials are replacing older ones, while more modern production technologies are resulting in greater precision and better quality.
Naturally, the same applies to our tail lifts. The best example is our innovative electronic control system which is not only far more superior to the older model, but also has more functions. This of course also increases the demands made on the specialists in our service centers who have to master the changes within the different tail lift models in ever shorter time periods. PALFINGER therefore organizes – right on site – ongoing professional and comprehensive training sessions to keep everyone on a high skilled level!
By using models, circuit diagrams, technical data sheets and diagnostics programs, our experts explain how equipment is constructed and how to troubleshoot more accurately supported by extensive training material.
At the end of the training, PALFINGER issues each participant a certificate stating that he or she has successfully completed the training. The participant is then considered a technical expert and is authorized to make regular inspections on tail lifts. The training is designed for specialized skilled staff who will perform maintenance and repair work on vehicles and vehicle accessories.
Staff participating in the training are already familiar with circuit diagrams and/or hydraulic systems and do repair work on vehicles or electro-hydraulic facilities. Trainers thus focus on the hydraulics and electronics of tail lifts. The training is supplemented by the use of demonstration materials, such as lift and closing cylinders, power packs with motor and pump, as well as valves, control boards, operating consoles and connectors.
Downloads
- The following overview contains the current available certificates according UNECE Regulation No 58 for rear underrun protective devices (RUPDs) – 03 series of amendments:
Cantilever
C 750 L
C 750 LX
PTC 750 L/LLW
C 750 S (1)
C 750 S (3)
C 750 S (3)
C 750 SLW
C 750 SPL/SPR
PTC 750 S
PTC 1000 LLW
C 750 LD – C 1500 ML
C 1000 SPL/SPR 1/3
C 1000 SPL/SPR 2/3
PTC 1000 L – PTC 1500 L
PTC 1500 S – PTC 2500 L
C 1000 S – C 3000 S
C 1500 SZ – C 2000 LZ
C 2000 SK – C 2500 SK
Foldable
F 1000 L
F 1000 SH – F 2000 LH
F 1000 SX – F 1500 L/LX
RETRACTABLE
R 1000 LM – R 2500 S
Vertical
V 1000 LQ
V 4000